
Rather than adjust speeds and feeds, Waveform automatically manages the width of cut of the tool, so the feed/speed remain the same. That means quicker cuts, removing more material, but just as critically, less wear on both the cutter and the machine.Įdgecam has built its own take on this technology (named Waveform) and built it into every appropriate strategy, so it’s a case of using them, once the feeds and speeds and other settings for your machine tools are dialled into the system. Loading on not only the cutter, but the whole spindle, is consistent and without those gut wrenching moves. How each vendor approaches this differs but the end result is the same. This means that large depths can be removed.

Edgecam Workflow allows the user to manually create toolpaths complimenting automatic toolpath generation
#EDGECAM SUBCRIPTION FULL#
Full flute with waveformsĮdgecam has its own take on the use of full flute machining techniques.Īs is now rampant across the industry, many are looking at this area to cut large chunks (metaphorically and literally) out of the machining cycle time by using the combination of cutting with the full (or near the full length) of the cutter with clever toolpaths to ensure that the cutter engages in a consistent manner with the material.įig 3.
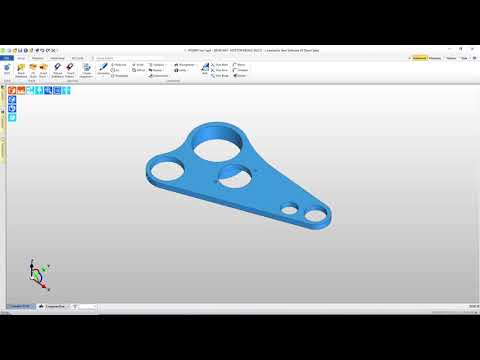
Then it’s a case of fine tuning things, ensuring there are no collision or gouging issues. Once in a fit state, the toolpaths are calculated. On the Planning Board, operations can be reordered prior to calculation, so things are as close to the final intent - way before calculation takes place. This selects the most appropriate cutter and operation for each set of features found based on the size of the part, the geometry and your settings.Īs you can see from both figures 1 and 3, this is displayed in a colour co-ordinated manner, splitting out each operation type (here, roughing is followed by profiling/finishing and then drilling cycles). It then uses its intelligence (again, based on your input to guide best practice) and creates a Planning Board of machining operations (found in the left hand panel of the UI). It looks for pockets, bosses (both open and closed), holes, flat faces and such. It begins by using Edgecam’s feature recognition tools to find machinable features using geometry analysis, rather than extracting features from the CAD part - allowing it to work with dumb geometry just as well as it does with native CAD parts. Again, Workflow is designed to run off the back of your own internal best practices, whether that’s by machine set-up (it’s perfectly suited to organisations running multiple, different machine tools), by geometry or by material. Once done, the process of extracting the machinable features from the part geometry begins. It also steps you through the definition of any jigs, fixtures, vices and clamps from predefined libraries.Īs with all knowledge-based systems, time spent setting these items up to match your best practices and available items, is time well spent. This can either be selected automatically based on part geometry or tweaked manually if there’s ambiguity. Workflow includes tools that allow the user to quickly import the geometry and define the correct datum.
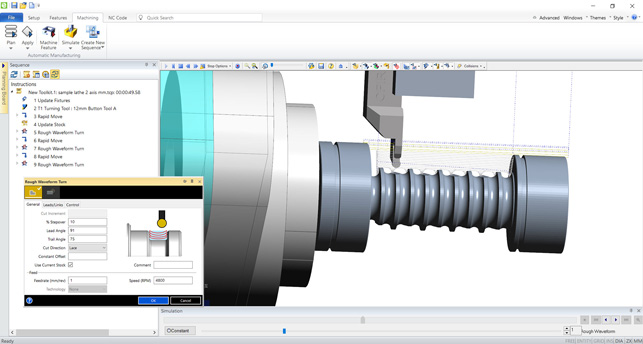
Full machine simulation allows Edgecam users to review the manufacturing process before it is sent to the machineĪs we’re all aware, geometry from the CAD system isn’t usually aligned (in terms of 3D co-ordinate space) in a manner that’s suitable for machining.
